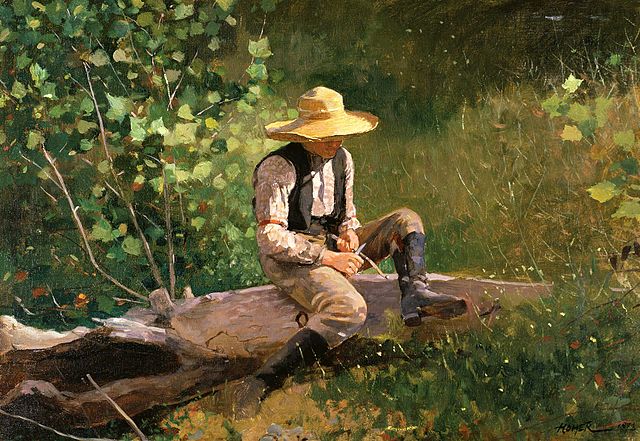
When you're looking for an oar carving knife, there are a few different things to keep in mind. Size, sharpness of the knife, stag bone, lamination, as well origins should all be considered when purchasing a knife. Learn how to choose the best one for you. This article will provide you with a guideline for choosing the right oar carving knife.
Size
Oar Carver series is a collection of carving pocket knife that are a timeless and iconic example of this craft. Three sizes are offered in the current lineup. Version 2 has a larger blade, and Version 3 has a thicker blade. Version 3 is slightly bigger with a wider gap and a thicker blade. Here are some tips to help choose the right size.
Sharpness
One of the most important aspects of any oar carving knife is the sharpness of its edge. The edge of any oar carving knife will eventually show wear such as dullness, chips and nicks. It is important to keep your knife sharp. It is quite easy to judge the sharpness and quality of an oar carving blade by looking at the edge. A magic marker can be used to match the angle between the blade's centre and the knife's edges.
One way to test the sharpness of an oar carving knife is to cut a piece of basswood across its end grain. The blade should cut through the wood with no drag marks or ripples. A smooth cut is like cutting a baby's bottom without leaving any marks. If the blade leaves these marks, it may not have the right edge for carving. Regularly check the sharpness and quality of your oar carving knife.
Laminated blades
The Oar Carver series, created by Ross Oar, a world-renowned knifemaker, is a classic example for the carving pocketknife. There are three versions currently: Versions 1, 2 & 3. Each version is quite different from the one before it. Version 2 for example has a greater difference between the two blades. It also has an edge that is thinner. The Oar Carver blade reference provides more details.
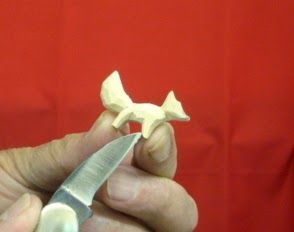
Mora makes the 106, and 120 versions. The Mora knife has a longer blade made from laminated steel. Both knives have a basic oval handle, and are also sold with a snap sheath. Another model, the Mora Frost 122 has a laminated steel blade and a 61 Rockwell high hardness. This knife is excellent for carving.
Origins
The Japanese oar carving knives were developed in ancient times. It is made of solid hardwood and has a narrow circumference, while the handle is four and a half inches long. The oar has an oar with a long, flat blade and a flat top. The knife's shaft measures 53 inches in length. The handle has been carved into a narrow circular shape, and the blade is separated from the shaft by a thin section made of wood.
Although the oar is the oldest known carving tool, its history goes back much further. The oar originated as a tool for riverine and coastal populations. Because of its widespread use and easy recognition, the Admiralty chose to use the oar symbol. However, the oar could have had many other meanings. Below are some examples of its origins. If you're interested, they can also be useful if your are curious about the history knife-making.
FAQ
Are there any other things I should know regarding woodworking?
It is easy for people to overlook the work involved in furniture making. The hardest part of the process is actually finding the right wood. It is difficult to choose between the various types of wood.
A problem is that wood doesn't have the same properties. Some woods will warp and others will split or crack. These are important considerations to make before you purchase wood.
What is the minimum investment a hobbyist needs to make in order to get started?
It is likely that you will need some capital in order to buy the required tools and supplies if your goal is to open your own woodworking business. A good place to start would be by buying a small table saw, drill press, circular saw, jigsaw, and sanding machine. These items don't cost much so they won't break your budget.
What kind of tools are used to carpenters?
Carpenters most often use a tool called a hammer. A hammer helps to carpenter pound nails into the wood. A hammer is used to hold pieces together during a project. Other tools include clamps and pliers, screwdrivers as well as measuring tape, pencils and saws.
What tools are best to begin with when I become a woodworker
Woodworking is an art that takes patience and practice. Learning how to use the various tools and techniques necessary for woodworking takes patience.
There are many kinds of woodworking equipment currently on the marketplace. Some prefer to use power tools, while others prefer to use hand tools.
It's your choice. But you should ensure that you pick the right tool. It may be a good idea to start with a basic set, if possible, if you don’t know much about hand tools.
You might also consider learning how to use the router to create intricate shapes from wood. These tools can be purchased at most hardware stores.
How can a woodworker start making money?
Many people want to open an online furniture business and are learning how to build it. If you are just starting to build furniture, there are many other ways to make money than selling on Etsy. Sell at craft fairs or other local events. A workshop could also be offered for people who are interested to learn how they can build their own furniture. If you have the experience to be a carpenter, builder, or a designer, you may consider offering your services in remodeling homes or creating custom pieces.
How do I determine what kind of wood my project is made from?
When purchasing wood, always check the label. The label should contain information about the wood species, its moisture content, and whether it has been treated with preservatives.
Statistics
- Most woodworkers agree that lumber moisture needs to be under 10% for building furniture. (woodandshop.com)
- Woodworkers on the lower end of that spectrum, the bottom 10% to be exact, make roughly $24,000 a year, while the top 10% makes $108,000. (zippia.com)
- Average lumber prices rose about 600 percent between April 2020 and May 2021. (familyhandyman.com)
- Overall employment of woodworkers is projected to grow 8 percent from 2020 to 2030, about as fast as the average for all occupations. (bls.gov)
External Links
How To
How to join hardwood without using nails
Woodworking is an enjoyable hobby. Woodworking is a relaxing hobby that allows you to use your hands to create useful things from wood. There are times when two pieces of wood need to be joined together. This article will teach you how to do this to keep your woodwork projects looking great.
Before you can join the wood pieces together, you need to remove any rough edges. You don't want to leave sharp corners that could cause problems later on down the road. Once you have done that, you can begin gluing your boards together.
If you're working with hardwood, you should only apply glue to one side. For softwoods like cedar and pine, glue should be applied to both sides. Press the boards down until the glue is fully incorporated. Be sure to let the glue dry before you move on to the next step.
Once you've glued your boards together you will need to drill holes in the joints to accommodate screws. Depending on what type screw you choose, the size of these holes will depend on how big they are. For example, if your screw is a 1/2-inch wooden screw, drill a hole that is at minimum 3/4 inches deep.
Once you have drilled your holes you will need to drive the screws through each joint and into the backside. Be careful not to hit the front surface of the board, or else you'll ruin the finish. Try to not hit the ends of the screws when driving the screws. This will prevent the wood from splitting.
Now that your project is finished, you'll want to protect it from the elements. You can either seal the entire piece of furniture or cover the top. Either way, you'll want to use a product that will last for years to come. Examples include oil-based varnishes and polyurethanes, shellac, lacquer and others.
These products can generally be found in any home improvement shop. You should make sure you are getting the right type for the job. Some finishes are toxic and should not ever be used indoors. When handling certain finishes, wear protective gear.