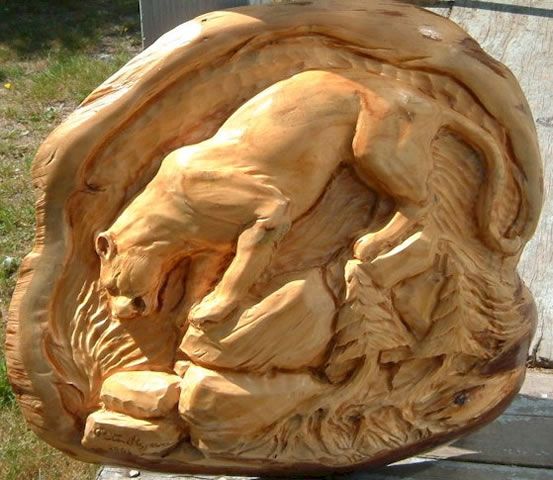
First, choose a piece and then make the required cuts to carve a face in wood. Using a step-by-step video, follow along as the expert guides you through the process. Carving the face will look more realistic if you use the progressing cut. The key to creating a lifelike visage is the progression of your noses on the piece of wood. You can add realistic details to your face by using colored dyes or shellac.
Hardwoods
Before carving a face out of wood, it is important to consider what type of wood you will be using. Hardwoods can be described as a group of trees with large leaves that can thrive in many climate zones. Hardwoods are suitable for various purposes due to their density, strength, appearance and versatility. While softwoods are more affordable, hardwoods can be durable and fire-resistant.
Softwoods such as butternut or basswood are good options for beginners to wood carving. These woods are easy to work with, and are great for beginners. But, softer woods may not be as durable or beautiful as hardwoods. It is important to try different wood types before you settle on one.
Softwoods
First, choose the type of softwood you want to use when carving a wood face. Softwoods are often more difficult to carve and have more knots. They are also more susceptible to breaking, particularly if you use large strokes. Beginning carvers will cut small pieces of timber, decreasing detail. It is not a problem but something to be aware.
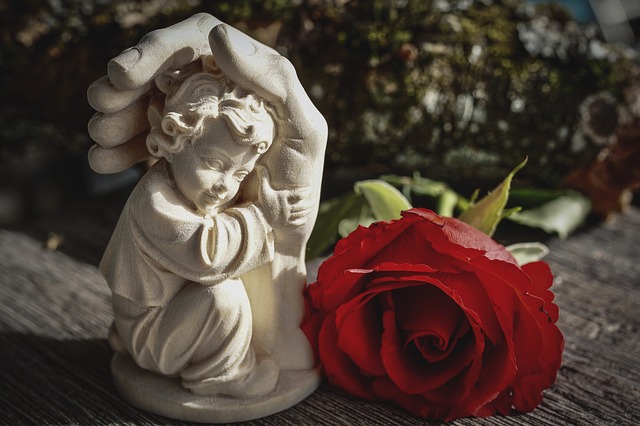
Some hardwoods are harder to work with than other. Aspen, butternut, basswood, and other hardwoods are some of my favorite to work. It is recommended to use knives with a higher bevel. Softwoods also make it easier to work with than hardwoods. This allows you to carve along or against the grain. The quality of your finished product will depend on the wood you choose for carving.
Colored dyes
To create a vibrant, detailed finish on a wood carving, try using colored dyes. These dyes can be purchased in many different colors. To create a unique color, you can add water or alcohol. You can also use shellac and colored dyes to lighten the wood. After applying dyes, ventilate your work area and clean your brushes with denatured alcohol. Paste wax is another option. Excessive glossiness can distract you from your work. To remove excessive glossiness, you can use 0000 steel Wool.
Wood dyes are available in several types and can be applied with ease. Wood dyes are compatible with all topcoats and are easy to apply. These dyes can also be used to solve common finishing issues. Because they come in a wide array of primary colors, they're easy to mix and apply. They can also be purchased in different shades so that you can create your own unique colors. They can be mixed to create new colors.
Shellac
It is important to have the shellac ready before applying it on your wood carving. A jar of shellac is available, but the best way to apply it to your wood carving is with a brush. A two-pound cut is sufficient. This is because it will grow slowly and will reduce the brush marks. It is better to get a thicker cut of shellac than one that is thinner, as it is extremely water-thin. Make a pad from small, golf-ball-sized pieces of cotton and lint-free cloth to ensure you get the correct amount. Next, dip your tip into the shellac. Let the excess water flow back into the bottle.
Shellac is used to highlight grain and give it color. Shellac is available as a variety colors. This allows you to mix and match different shades of resin to create your own blends. The lac can be used to darken the color. Shellac, unlike other wood finishes won't turn yellow or become cloudy. It will also last longer, so you can make more faces. This is possible with any type of wood carving project.
Gouges
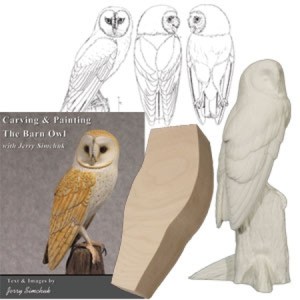
You can find a wide variety of sizes and shapes in gouges. Straight and palm gouges are two of the most popular types. Straight gouges can only be held with one hand. Palm gouges, on the other hand, have shorter shafts. Hand held carving is easier with the shorter handles. The palm gouges, also known as veiners, are great for carving wood faces. Here are a few things to consider before you start carving.
First, you should know how to choose the right gouge. The gouge should be capable of carving a small v-shaped groove. A sharp edge and small sweep are essential features of a good gouge. Gouges can be categorized by their size. A 3/10-inch gouge will produce the same size cut as a 5/10-inch gouge. The scoop between the edges gets deeper as the first number is increased and the sweep becomes more curvy. A small gouge can create a profile with a narrow sweep.
FAQ
How do you calculate woodworking costs?
Remember to keep costs as low as you can when calculating project costs. It is important to ensure that you are getting the best materials prices. It is important to take into consideration all factors that can impact the cost of your projects. These include time, skill and experience. You can find an estimate of the cost of different woodwork projects in our guide to common DIY tasks.
What's the difference?
Hobbyists like making things with wood. Professionals focus more on quality. Hobbyists are proud of their creations and will often share them with family members and friends. Before they start working on a project, professionals will spend hours researching the designs. Professionals will be meticulous about all aspects of their work, from selecting the right materials to finishing it.
How much will it cost to get started?
Each project is unique so there aren’t exact numbers. These factors will help you get an estimate of how much money is needed.
-
Cost of materials
-
Tools and equipment
-
Time spent on the project
-
Your hourly rate
-
How much profit can you anticipate to make
-
You can hire help, regardless of whether you have a plan.
For those just beginning, it may be a good idea to start small with simple items like boxes and picture frames. As you gain experience, more difficult projects will become possible.
Statistics
- The best-paid 10 percent make $76,000, while the lowest-paid 10 percent make $34,000. (zippia.com)
- If your lumber isn't as dry as you would like when you purchase it (over 22% in Glen Huey's opinion…probably over 10-15% in my opinion), then it's a good idea to let it acclimate to your workshop for a couple of weeks. (woodandshop.com)
- The U.S. Bureau of Labor Statistics (BLS) estimates that the number of jobs for woodworkers will decline by 4% between 2019 and 2029. (indeed.com)
- Overall employment of woodworkers is projected to grow 8 percent from 2020 to 2030, about as fast as the average for all occupations. (bls.gov)
External Links
How To
Tips on how to drive a nail in wood
It is essential to pick the right size and style of hammer before you can drive a nail in wood. There are many types of hammers that you will find: claw hammers and sledgehammers; mallets; ball peen hammers; and hatchets. Each type of hammer comes with its advantages and disadvantages. A clawhammer works best when hitting something hard like nails. However, it can sometimes be difficult to see exactly where the strike is going. A sledgehammer is great for hitting large areas at once, but it's too heavy to use effectively for smaller tasks.
Place your hand flat on the side of your chosen hammer so that the handle rests in your palm. Hold the handle in your hand, but don’t force it too hard that you break. The hammer should be held straight up with your wrist relaxed. Now, move the hammer towards the center of the nail by swinging it back. You should feel the impact of the hammer striking the nail. You can practice swinging the hammer with a block or wood until you feel the rhythm.
When you're ready to start driving the nail, hold the hammer in front of you close to your body. To ensure that the nail is perpendicular on the surface of the wooden floor, position it. Keep your focus on the tip of each nail. Swing your hammer forward. Then follow through with the motions of the hammerhead. You can repeat this several times, increasing your swing speed. Once you've mastered the technique, try adding power to your swings. Try holding the hammer above your shoulder and bring it down forcefully. This will help you put more energy behind each of your moves.
After you have nailed the hole, take the hammer off the nail. To pull out the remaining nails, use a screwdriver or pry bar. To avoid splitting the wood, make sure the nail heads are not touching the board's surface.