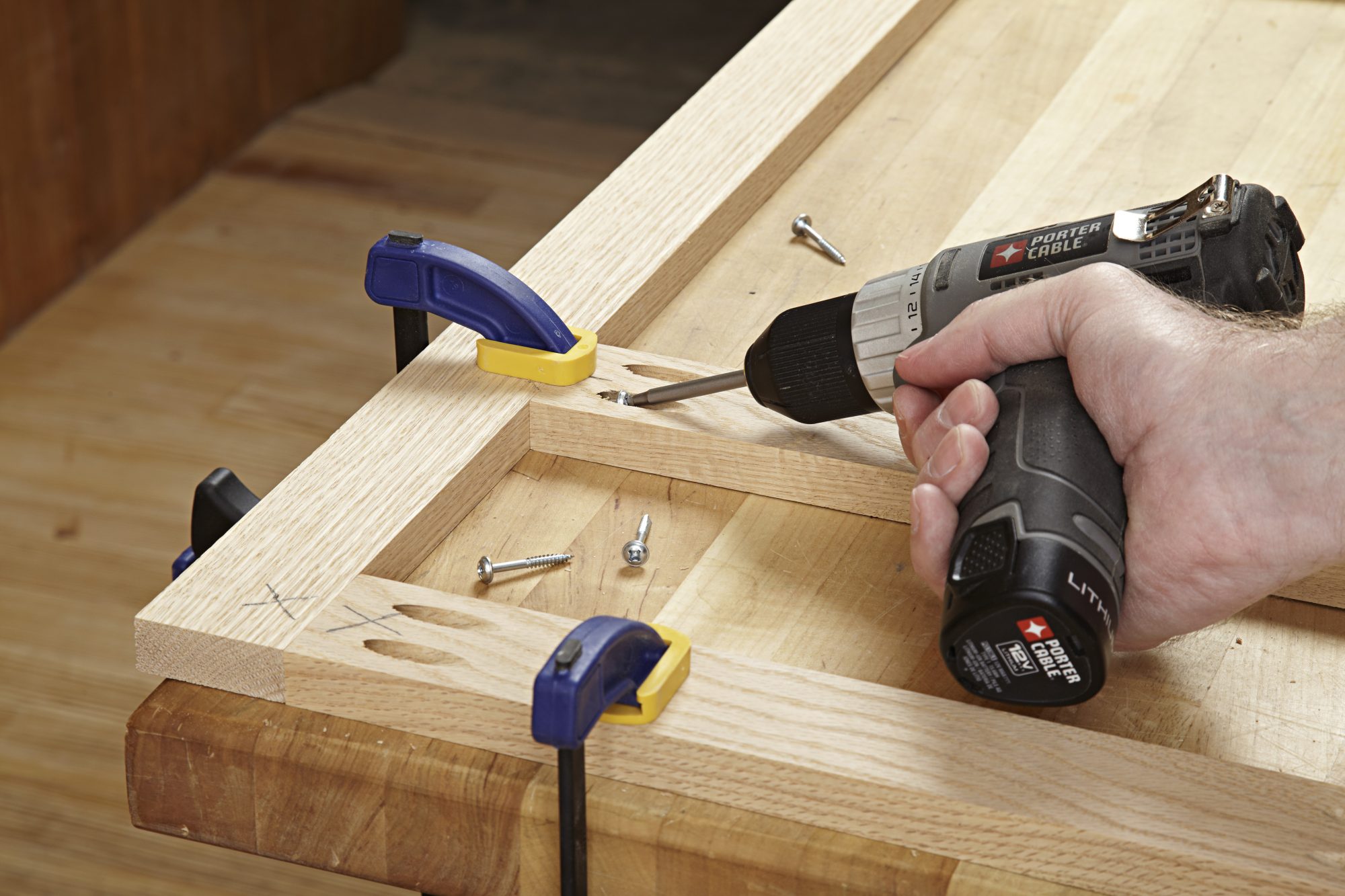
It can be difficult cutting rough lumber and loading it into your car is not easy. Bring your tape measure, hand saw and saw to the hardware store. Also, make sure to buy extra boards in the event that the one you have purchased doesn't fit. Also, be sure to purchase the board with checks and knots, as they may not get planed down as you expect. You don't want the board to be ripped and you have to start over. It will take time and cost you money. So, it is a good idea to buy a few extra boards.
You save more
A sawmill can turn 59% to 50% of rough lumber into boards by cutting it. The remainder of the log can be considered waste, including sawdust, bark, chips and chips. Although a less perfect cut can result in more waste than a perfect cut, it should still not exceed 20%. Here is a simple formula that will estimate how much wood has been wasted in a given board. For a nominal 4-foot board, the sawmill should remove about 18% of its volume to achieve the desired lumber thickness and width.
Rough lumber is not always available in standard dimensions. The dimensions of hardwood bought from a big box store are often known, allowing you to plan your project around the standard size. This means that the edges of rough lumber are not always straight, which can lead to waste. Additionally, rough-cut lumber often requires a common width which results in a lot wasted lumber. This waste cannot be reused later.
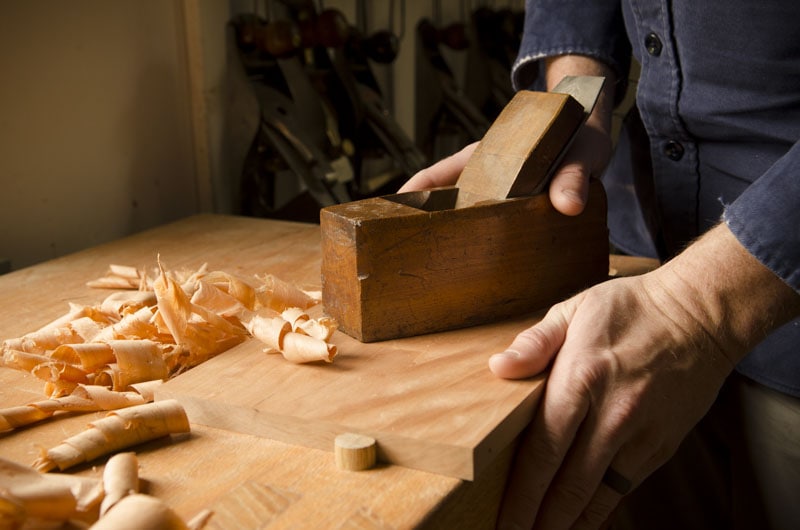
Preparation
To prepare for cutting rough lumber, the first step is to measure the length. Rough lumber may not arrive at the lumber yard perfectly flat. It may not have parallel sides or edges. This may mean that it will take several passes to flatten. It is a good rule of thumb to take out 1/16" per pass. If your lumber has concave sides, it is best to run it through the circular saw with the concave edge down.
The rough cut lumber should generally be flattened to 1/4" before the saw cuts. After flattening and sanding the face, plane it to the thickness of your finished board. Measure the length and width of the finished lumber once you have determined the thickness. Make sure to account for any imperfections. Plan your project around the boards available. Do not buy lumber that is uneven. It will be difficult to work on boards that are bowed, warped or twisted.
Cost
There are two types if lumber: rough-sawn lumber and dimensional lumber. Home improvement stores generally carry finished lumber but very rarely rough-sawn. Both types of lumber are typically carried by local sawmills or lumber yards. The only difference between these two types lies in the work involved. Because it takes less work to make, rough-sawn boards are more affordable. It's also much wider and more thin than finished lumber.
Although it's generally more affordable to buy lumber from a lumber yard or mill, standard lengths are less common. You can mill your own lumber for a cheaper alternative to purchasing rough-sawn lumber. However, you will need more shop space and higher power. Milling equipment can be noisy and requires training. It is important to know the laws that govern your locality if you plan on using your mill.
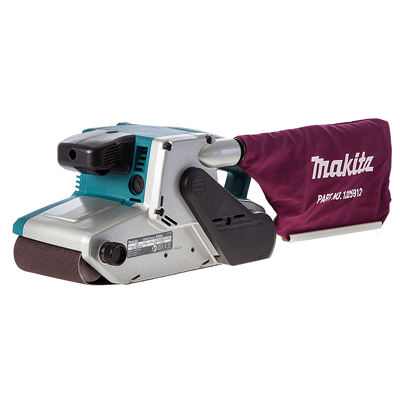
Source
There are many options when it comes to buying lumber. There are many different sizes, shapes or finishes that you can choose from. Rough sawn lumber, by example, is unfinished lumber. It has been cut into boards. This lumber tends be more sturdy than other types, as it has more moisture. Additionally, it is thicker that surfaced wood. The following are some benefits of using rough sawn lumber for your woodworking projects.
The first benefit is its availability and low price. Rough lumber isn’t treated and is not typically sold at a hardware retailer. However, this type of lumber has its pros and cons. It is generally cheaper by volume, but costs more per board foot to transport. It takes longer to finish than treated wood. So, you might want to consider this option when you're deciding how much lumber to buy. For projects that will require rough sawn lumber, you might want to purchase a large amount and some for finishing.
FAQ
What is the main difference between plywood or particle board?
Plywood consists of layers made from wood and pressed together by pressure. Plywood is available in a variety of thicknesses. It is often used to make cabinets or flooring. Particle board consists of sawdust mixed and resin. The resin is then compressed into large blocks. This board is commonly used in home improvement projects. Both boards are strong and can be easily cut.
What woods are suitable for making furniture?
Woods are classified according their hardness. Softwoods include cedar, pine, cedar, and Cypress. Because they are resistant, they can be used for outdoor furniture. Hardwoods include oak, maple, mahogany, and teak. They can't withstand the elements outside so they're best kept indoors.
What is the average time it takes to finish furniture?
It depends on which wood you choose, how complicated your design is and what amount of finishing you apply. Hardwoods, for example, require more maintenance than softwoods. Hardwoods can also be more costly than softwoods. But they last longer, and resist moisture better. Finishing furniture can take anywhere from one week up to three months.
What would you recommend as a starting material for woodworking?
Start with softwoods such as pine and poplar. Once you feel comfortable with these two, move on to hardwood.
Statistics
- Average lumber prices rose about 600 percent between April 2020 and May 2021. (familyhandyman.com)
- Woodworkers on the lower end of that spectrum, the bottom 10% to be exact, make roughly $24,000 a year, while the top 10% makes $108,000. (zippia.com)
- The best-paid 10 percent make $76,000, while the lowest-paid 10 percent make $34,000. (zippia.com)
- Most woodworkers agree that lumber moisture needs to be under 10% for building furniture. (woodandshop.com)
External Links
How To
How do you measure wood accurately?
Wood measurement can be done using several methods. We use a digital caliper (a tool used to measure distances), a laser level (used to make sure your work surface is flat), and a bubble level (used to make sure your work surface is perpendicular).
Two jaws are available on a digital scaler. One can open and the other close. One jaw holds a measured object and the other measures distances between the points. Digital calipers are great for measuring small distances, such as thicknesses of wood.
Laser levels have an infrared light beam that projects a line across the floor. The laser emits red dots on the line. By looking down the line, you can see whether the surface is even or not. For large surfaces, laser levels are the best way to check their accuracy.
Bubble levels look similar to a compass. There is a bubble at the center of this device. The device will indicate whether the surface is level as long as it is centered. Bubble levels can be used for checking the accuracy in smaller areas.